RFID Applications in Steel Manufacturing Plants
13/07/2025
Unlike other manufacturing sectors, the steel industry operates in highly specific environmental conditions. Products such as steel coils and sheets are often produced in high-temperature environments, and their metal composition poses technical challenges to the transmission and reception of RFID signals.
To effectively implement RFID in this environment, it’s essential to understand the product characteristics and the technological limitations involved. This understanding helps in building the most efficient solution — both in hardware and software.
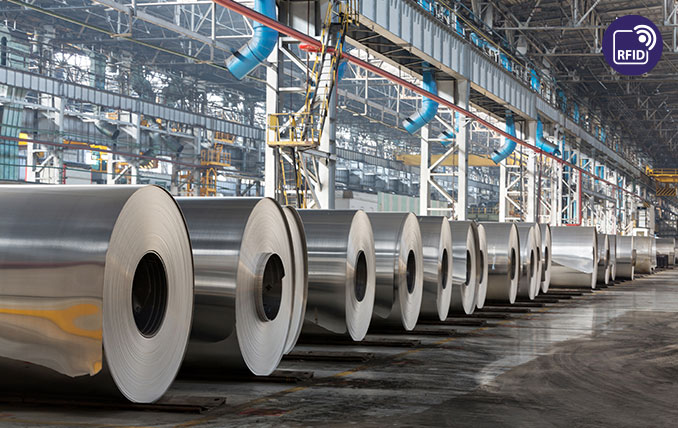
Challenges of Traditional Management Methods
Traditionally, steel factories rely on barcode technology to read product and material information. However, barcodes have several limitations in terms of reading direction, distance, and data storage capacity. Moreover, barcode labels are easily affected by environmental conditions and can be damaged during handling.
While the initial investment in barcode systems may seem lower, there are hidden operational costs. For example, poor signal reception may result in unreadable barcodes, forcing staff to spend extra time manually locating products. This leads to time-consuming inventory counts, delays in inbound and outbound logistics, and longer truck waiting times at loading docks.
Another challenge is that steel products are usually large and heavy, making it difficult to locate and scan small barcode labels. Operators may struggle to access tags or move items, which increases both the complexity of the task and the risk of workplace accidents.
Applying RFID to Steel Manufacturing Operations
RFID technology addresses these challenges by attaching RFID tags directly to finished steel products. Handheld RFID readers can assist workers with inventory checks, while fixed RFID gates can monitor the movement of goods at controlled access points.
RFID readers can capture signals from a distance and in multiple directions, even in high-temperature environments. This capability reduces inventory tracking and product searching time by up to 90%, while maintaining over 95% data accuracy. As a result, warehouse operations become faster, and overall workflow efficiency improves significantly.
Considerations for Choosing RFID Tags for Steel Products
Because steel products are made of metal, they can interfere with RFID signals. It’s crucial to study the product characteristics — such as size and material — in detail to choose the appropriate RFID tags. These should be specialized tags designed for metal surfaces.
Example: RFID Implementation Workflow in a Steel Manufacturing Plant
- RFID Tagging
An RFID tag is attached to each finished steel coil. - Product Identification
When products are released from the warehouse, operators use handheld RFID readers to retrieve product data such as ID, size, type, and weight. - Logistics Tracking
When products are loaded onto trucks, warehouse staff can continue the tracking process using fixed RFID readers or mobile devices to confirm shipment details and update the system in real-time.
This approach not only improves inventory accuracy and operational efficiency but also enhances safety for workers and reduces unnecessary labor. If your business is considering RFID for steel manufacturing or similar industries, contact 1Gate for a tailored consultation.
📧 Email: info@1gate.com.vn
📞 Phone: (028) 3932 0445
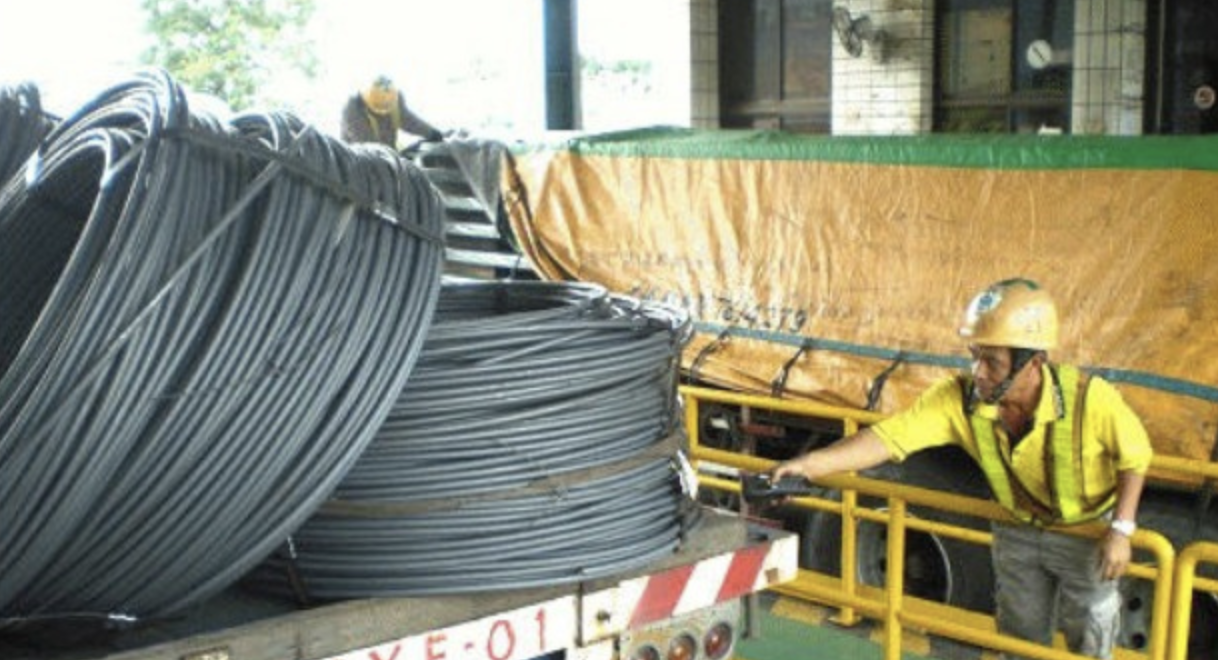
Related Articles
- 1Gate’s RFID-Based Traceability & Anti-Counterfeiting System
- Hệ thống truy xuất nguồn gốc và chống giả 1Gate
- Choosing RFID Tags for Metal Surfaces – What You Need to Know
- UNIQLO Implements RFID on a Global Scale
- Walmart, RFID, and the New Retail Strategy
- Ứng dụng RFID trong nhà máy sắt thép
- Lựa chọn thẻ RFID gắn trên kim loại- Những điều cần lưu ý
- UNIQLO áp dụng RFID trên phạm vi toàn cầu
- Wallmart, RFID và chiến lược New Retail